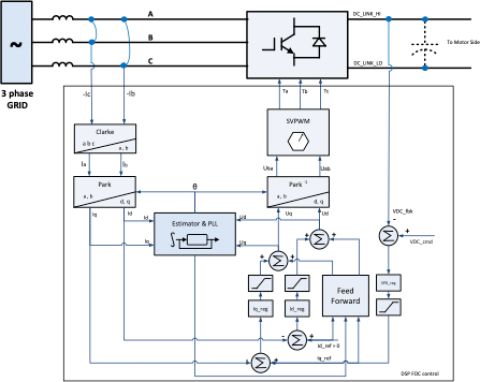
Calnetix offers power electronics and controls design and manufacturing. Vericycle™ Bidirectional Drives or Adjustable Speed Drives are the ideal choice for any type of high-speed rotating machinery. Calnetix offers both off-the-shelf and custom high frequency variable speed drives and inverters and is committed to working in collaboration with our clients to deliver the highest quality products. Some of the key advantages of the Calnetix Vericycle™ VFDs include:
Calnetix’s Bidirectional Drives are optimized with the whole system in mind. In particular, the variable frequency drives have features that maximize the efficiency of the power electronics, which in turn reduce the losses in the machine that is connected to the drive, increasing overall efficiency:
Space vector modulation
Dynamic deadtime insertion in the switching patterns of the power devices
Low total harmonic distortion (THD) of the machine currents and grid side currents
Optimized back electromotive force (BEMF) for the required DC bus voltage of the variable frequency drive and the grid voltage
Introduction of SiC inverter switching device
Calnetix’s high frequency variable speed drives are an ideal choice for low-impedance and high-speed machines due to the following:
High switching frequency that is synchronized to the fundamental frequency of the machine
Dynamic deadtime insertion in the switching patterns of the power devices
A simple inductance filter, which further reduces the distortion of the current that is drawn by the machine and limits the maximum distortion of the machine currents
Higher switching frequency to reduce the motor current harmonics, which reduces the overall operating temperature of the stator and rotor components of the machine
The Calnetix power electronics grid tie sensorless controller is a space vector modulated inverter connected to the three-phase grid through one series inductance per phase, which acts to reduce the switching harmonics entering the grid. Large inductance and high switching frequency are used to minimize the switching harmonics into the grid. The control benefits include:
Robustness and stability across a wide range of operating conditions
Good tolerance to the grid voltage unbalance and wave form distortion
Eliminates the requirement of complex rotor position sensing device, such as resolver, which simplifies the motor design
Sense cable routing and breaking during operation, which is one of the major reliability concerns. Sensorless architecture of variable frequency drive eliminates this concern, thus improving operating reliability
Two major control loops – inner current control (to regulate the magnitude and phase angle of the current to and from the grid) and outer voltage control (to regulate the DC bus voltage to the predefined value)
D-axis and Q-axis currents are de-coupled and then regulated separately by current controllers
Ability to transfer current (power) from the DC bus to the grid with unity power factor, and vice versa
Ability to adjust the reactive current (power), if required
Ability to provide better noise immunity and track grid frequency and angle smoothly due to a virtual flux estimator with a phase lock loop (PLL)
Ground fault protection
Anti-islanding and other grid interface protection through external protective relays
Calnetix offers fully bidirectional AC VFDs by using an active grid-tie inverter in addition to the motor drive inverter. This allows both motoring and generating applications to be seamlessly implemented without requiring any additional hardware, such as a dynamic braking resistor.
Both motor drive inverter module and grid-tie inverter module are identical in construction sharing a common DC link capacitor. This offers a highly modular low parts count design.
While most motor drive inverters are inherently bidirectional, many variable speed drives utilize either a fully passive (diode-bridge) or semi-controlled (SCR bridge) grid converter. These converters are unidirectional, meaning they are only capable of providing energy flow in one direction. While this approach may be suitable for pure motoring applications that utilize a dynamic brake resistor for motor braking, this approach does not work for generating applications.
Calnetix’s variable frequency drives produce low total harmonic distortion (THD) in both the motor and grid side currents. Limiting the maximum distortion in the currents drawn from the grid and by the machine in effect minimizes THD, which is important since harmonic currents produce additional losses and heat in the machine, but do not produce useful torque. Grid operators typically have requirements for the maximum allowable THD that is produced by grid-tied inverters, so it is important to limit the maximum THD that is produced by a VFD. The same attributes that make Vericycle™ adjustable speed drives perfect for low-impedance and high-speed machines also allow them to produce low THD. These attributes include:
Switching the power devices of the inverters at a high frequency that is synchronized to the fundamental frequency of the machine
Dynamically adjusting the deadtime that is inserted in the switching patterns of the power devices
Simple inductance filter for both grid side and motor side inverters
Extremely fast pulse by pulse current limiting and overcurrent protection feature
Reliability and long operating life are a top priority in the design of Calnetix’s power electronics drives. The reliability of Calnetix variable speed drives is increased by the following:
Keeping the electrical and thermal stresses on the components within the drive to reasonable levels
Reducing the parts count in the AC VFD
Not requiring position feedback from the machine and voltage feedback for the machine and grid
Rigorous electrical and thermal testing before the variable speed drives leave our factory, minimizing manufacturing and component infant mortality issues
Calnetix variable frequency drives incorporate sensorless space vector modulation to increase the utilization of the internal DC bus of the drive. A high DC bus utilization is particularly important for optimizing the efficiency of the VFD and machine, since it allows the back electro-motive force of the machine to be increased. This leads to lower machine currents, and therefore, lower losses in both the drive and machine. The variable frequency drive is sensorless in the context that no physical sensor for the machine rotor position is required. Calnetix’s power electronics utilize a virtual flux estimator and phase lock loop instead of a voltage estimator for determining the machine rotor position. A sensorless AC drive provides the following benefits:
More reliable and less prone to high frequency electrical noise from the machine
Requires fewer parts compared to a drive that requires position feedback
Better noise immunity compared to a voltage estimator
Excellent dynamic response
Relatively insensitive to disturbances in the line voltage
Able to track the position smoothly through zero-speed
Maximizes the efficiency of both the VFD and connected machine
Calnetix’s variable frequency drives can incorporate either an active or passive front end to meet the technical requirements and cost target of an application. Typically, Calnetix’s variable frequency drives are equipped with an active front end (grid-tie inverter). This allows for bidirectional flow of power. An active front end also decouples the machine side inverter from the grid since the DC bus voltage in the VFD does not vary with the grid voltage. As a result, a drive with an active front end is able to be interfaced to U.S. and international power networks (50 and 60 Hz) without having to modify the design of a machine connected to the drive. For applications where unity power factor and low THD is required, an active front end is necessary.
A passive front end (rectifier) in which the DC bus varies with grid voltage is an alternative for applications that only require a unidirectional flow of power into the variable speed drive from the grid. A dynamic brake resistor can be added to a variable speed drive with a passive front end for fast deceleration of any attached machine or for protection of the drive for applications with high inertia loads.
Calnetix has developed multiple control boards targeting different applications. The latest control boards use NXP automotive grade microcontroller unit (MCU) MPC5744P. It features dual-core Power Architecture in delayed lock step mode for mission critical safety applications. The MCU execution speed can be up to 200 MHz with 2% frequency modulation to reduce electromagnetic interference (EMI) noise. The operating temperature is up to 125 °C.
Calnetix’s technological innovations in high-power transistors and permanent magnet motors have increased power capability, reduced size and cost, and made new applications feasible. From electric motor applications to position control applications, Calnetix’s motor drives and inverters adjust to the needs of the process and help increase the overall efficiency of the system. Calnetix currently offers the following variable speed drive and inverter solutions.
Vericycle™ 75
Vericycle™ 300
Vericycle™ 300-AE
Vericycle™ 450
Vericycle™ 600
Vericycle™ DC-1200
Electrocycle™ DC-150
Enercycle™ DC-1000
Machine Voltage: 0-480 VAC
Machine Current: 60 A (CONT)
Machine Phases: 3
Machine Frequency: 0-2000 Hz
Enclosure Type: NEMA 1
Grid Voltage: 380-480 VAC
Grid Current: 60 A (CONT)
Grid Phases: 3
Grid Frequency: 50-60 Hz
Calnetix is uniquely positioned to offer custom solutions by leveraging our existing technology and advanced engineering capabilities to deliver custom AC VFD designs that are cost-effective, robust, and delivered on time. Some of these capabilities include:
Robust control algorithms that are applicable to a large range of applications
Flux-based estimator that provides very robust sensorless control of a machine connected to the variable frequency drive
Flexible system architecture, including fully bidirectional operation
Design experience in both adjustable speed drives and permanent magnet synchronous machines that allows for anticipation of risks in a new design
Custom packaging and enclosure designs to meet the harshest of environments and to meet weight and space requirements
Fully integrated team of engineers who are well versed in power electronics design, controls design, embedded software engineering, EM design, thermal design, mechanical stress analysis, materials engineering, and compliance engineering