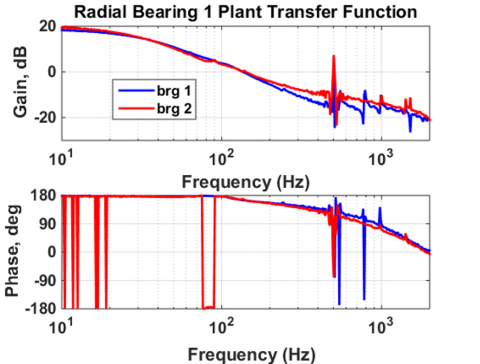
Calnetix offers Powerflux™ Magnetic Bearings in radial and side-by-side combination configurations and Xcelflux™ Magnetic Bearings with a unique coil architecture. The unique advantages of these active magnetic bearings (AMBs) include the following:
When designing high-speed rotating machinery, Calnetix’s active magnetic bearings afford unique advantages over conventional roller or fluid-film bearings. Unlike conventional bearings, AMBs suspend the target rotor in a magnetic field, creating a non-contact rotor support system with extremely low friction and no contact wear.
Some benefits of contactless magnetic bearings include:
Calnetix utilizes an adaptive synchronous force rejection algorithm to minimize vibration transferred from the rotor to the housing. Low transmitted vibration is important in high-precision applications like those in the food, medical, and defense industries.
The benefits of low-vibration transmissibility include:
Calnetix’s active magnetic bearing (AMB) products allow the user to monitor the health of all aspects of the magnetic bearing system. Calnetix’s AMBs include a position sensor, a magnetic actuator, and a microcontroller, which allow the user to access machine health monitoring and diagnostics information. Connect to an external computer to easily identify, analyze, and archive the health and historical performance of the machine via advanced diagnostics. Furthermore, adding Calnetix’s high-frequency data capture hardware and interface can enhance health monitoring capabilities.
Some of the health-monitoring features include:
In most cases, Calnetix leverages its broad multidisciplinary in-house expertise to work with a customer to design an entire machine on magnetic bearings from the ground-up. This approach is far more effective than simply supplying magnetic bearing components. Calnetix has found that this approach achieves optimal machine performance as an integrated system and fully realizes the magnetic bearing system potential.
Some of Calnetix’s competitive advantages include:
Calnetix has developed a novel Graphical User Interface (GUI) to give both end users and specialists an intuitive way to interact with the inherent benefits of a magnetic bearing system. Furthermore, Calnetix has undertaken a continuous improvement process to refine and upgrade the GUI by incorporating feedback from both internal and external customers. The GUI provides insight into all aspects of magnetic bearing and machine performance.
The GUI is the platform for system setup, monitoring, and diagnostics, including the following:
Powerflux™ AMBs utilize homopolar permanent-magnet-bias magnetic fields in conjunction with an electromagnetic field. In contrast, Xcellflux™ AMBs use heteropolar electromagnetic bias fields in conjunction with electromagnetic control fields. Both products are low-cost and easy to assemble, as shown and described below.
PowerFlux™
XcelFlux™
Magnetic bearings do not function independently; they require multiple precision components to work together in a unique system. Calnetix has carefully designed and developed all of the active magnetic bearing system components, as described below.
The actuator in an active magnetic bearing is the electromagnet that applies a controlled force to the shaft of a machine to control its position. A radial actuator consists of a lamination stack with control coils and poles arranged to give two orthogonal axes of control. Conventional AMB actuators produce a linearizing flux using a DC current. However, Calnetix actuators use a permanent magnet arrangement to produce a linearizing bias flux. This leads to lower losses, lower complexity, and improved compactness. Two other common actuator configurations are a combination radial/axial actuator and a stand-alone axial actuator.
An AMB actuator must be connected to a Magnetic Bearing Controller (MBC) which supplies the control current to the coils based on a position sensor feedback signal and a control algorithm.
Check our detailed PM Bias Resource Page to learn about the operational principles of a homopolar, permanent magnet-biased active magnetic bearing.
Position sensors are critical components of any active magnetic bearing. Their role is to continuously provide the controller with accurate up-to-date information about the rotor position unaffected by the external factors. They must be immune to external factors such as speed, temperature, dust, working fluids, external magnetic and electrical fields, etc.
Significant progress has been made in developing self-sensing AMBs, that combine position measurement and force generation functions into one physical component. However, such combination units have fundamental performance limitations, likely limiting their use to low-cost, low-speed machines. A conventional bearing arrangement utilizing dedicated radial and axial sensors will likely remain dominant.
Different types of position sensors have different property combinations, making some more suitable for specific applications than others. In industrial-use environment, it is typically preferable to have one technology that covers as many applications as possible. When considering the wide breadth of available technologies, such as optical, capacitive, and electromagnetic position sensors, electromagnetic position sensors are the most universal solution.
Calnetix utilizes four types of sensors, depending on the application specifics:
All sensors include the sensitive element (sensor head) integrated into the machine, where the displacement needs to be measured. Conversely, the sensor electronics are typically located in the Magnetic Bearing Controller (MBC).
A speed sensor provides the active magnetic bearing with information about the rotational speed and angular position of the rotor. This information is required to adjust the control parameters as speed changes to enable the rotor unbalance cancellation. Calnetix uses two types of dedicated speed sensors. Both sensors utilize a source of a DC magnetic field and a Hall-effect element that measures that field. They also contain additional rotor features, such as a notch which modulates the magnetic field.
Backup bearings support the rotating assembly when the magnetic bearing system is deactivated. They also provide rotor support in the event of an overload of the magnetic bearings or a failure of one of the components. During normal operation, the backup bearings are inactive, and have a small radial and axial clearance to the rotating assembly. This radial clearance is, usually on the order of 0.003”-0.009”.
Calnetix’s most common backup bearing configuration is two Duplex stainless-steel pairs of angular contact ball bearings preloaded face-to-face (DF). This mounting configuration requires the bearing outer races to be clamped – either rigidly or via a spring – on the outer race of the bearing. Hybrid bearings are available as backup bearing options, typically fabricated from conventional SAE 52100 steel races and SiN3 balls. Backup bearings for high-speed active magnetic bearings are usually cageless and use either a grease film, dry film lubricant or a light grease fill.
Calnetix Technologies has developed and deployed advanced Magnetic Bearing Controllers (MBCs) that contain all of the elements necessary to operate magnetic bearing systems.
The company currently produces two MBC platforms in the Insight™ series and one in Concurrence™ series.
For more information, visit the Magnetic Bearing Controllers product page.
The Calnetix Service Graphical User Interface (GUI) is used for system setup, monitoring, diagnostics and system identification. The upper half of the front panel, shown below, displays orbit plots from the two radial bearing sensors as well as a time history plot from the axial bearing sensor. Other operating variables shown on the GUI include spin speed, static current, and synchronous displacement and current. Status variables, such as levitation and fault status, are also indicated on the GUI. Finally, a System Information window on the right gives version information for the GUI, firmware, parameter file and machine serial number specifier.
More detailed information displays and functionalities can be accessed through the action buttons: Digital Signal Processors (DSP) Actions, View Logs, Fault Summary, View/Set Parameters and Measurements.
Such additional functionality includes the following:
Active Magnetic Bearings (AMBs) have been used in commercial rotating machinery for over 30 years because they offer excellent performance over long operational lifespans. This is possible because they operate with few friction elements and no wearable parts or components. In recent years, OEMs have increased the adoption of magnetic bearing systems, leading to significant lifecycle cost reduction and increased market penetration across diverse industries.
To learn more about these and additional advantages Calnetix AMB systems can offer your application, visit our AMB Resource Page.
How Magnetic Bearings Work
How A Magnetic Bearing Controller Works
Advantages of Magnetic Bearings
Transient Simulation of Magnetic Bearing and Backup Bearing Interaction in a High Speed Rotary Atomizer Subjected to Impulsive Loads
Design and Shop Testing of a 165kW Cryogenic Expander/Generator on Magnetic Bearings
Comparative Study of Axial/Radial Magnetic Bearing Arrangements for Turbocompressor Applications