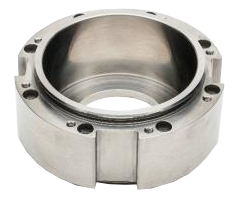
Calnetix’s passive magnetic bearings offer various advantages, such as high reliability, low losses, no active control and the ability to function in vacuum environments. Some of the advantages of PMBs are described below.
Calnetix’s passive magnetic bearings allow for zero-friction support of the rotating shaft. The benefits include:
Calnetix's Passive Magnetic Bearings Utilized in Affiliate Company Product
Calnetix’s PMBs have a simpler construction compared to conventional bearings. This can lead to the following benefits:
Low manufacturing cost
No additional pump or cooling mechanism required for lubrication
Compared to conventional mechanical bearings, PMBs can be easily integrated into turbomachinery and provide the following benefits:
Simpler and compact electronics allows easy integration inside a machine with only two wires emerging out to provide power
Low power consumption at operating speeds
High-temperature operation
Calnetix’s PMBs are highly reliable and low complexity bearings that can be used across many industries. By eliminating the need for lubrication, as well as the need for any active components, the PMB provides long-term, maintenance-free operation. Features of Calnetix’s PMBs are shown and described below.
Duraflux™
Calnetix’s PMBs generally have larger radial clearance (over 20 times) between the shaft and the bearing stator compared to mechanical bearings
PMBs can be used in conjunction with active dampers to eliminate the cross-coupled forces generated due to eddy currents induced on the rotor sleeve
PMBs are impervious to issues, such as pitting and imbalance that can affect the performance of traditional mechanical bearings
Magnetic bearings do not function on their own; they require multiple components working together as a unique system. Calnetix has designed and developed all of the components that make up the passive magnetic bearing system, and these components are shown and described below.
Rotating machines use radial dampers to damp radial rotor movements in order to stabilize rotordynamic modes and limit the unbalance response of the shaft. Conventional mechanical dampers provide large damping but have large rotational losses, and the amount of damping is not easy to adjust as it can cause high housing vibrations. Active magnetic bearings can take care of most of the problems listed above, however they can be complicated and expensive to manufacture. Calnetix has developed an active electromagnetic damper that provides a medium level of adjustable damping without an external control system. They are simpler in construction to an AMB and less expensive. An active electromagnetic damper also minimizes the total energy dissipation due to rotor unbalance. When used in conjunction with PMBs, they provide robust non-contact rotor support in applications where active magnetic bearings are not a viable option. Active electromagnetic dampers have simple and compact electronics and are easily installable in limited space rated for high temperatures. They generally have low power consumption at operating speeds.
The active radial electromagnetic damper consists of magnets mounted on the rotating shaft surrounded by velocity sensing coils placed in proximity of the rotor. As the rotor moves radially, voltage is induced across the sensing coils proportional to the lateral velocity of the rotor. A transconductance amplifier circuit generates electrical current in the actuator coils proportional to the voltages induced across the velocity sensor coils. The electrical current in the actuator coils induces a magnetic field that interacts with the rotor to damp the radial movement. The active electromagnetic damper can be designed to fit a particular application, such as to help damp low frequency rotordynamic modes and ignore unbalance excitations at high speeds.
PMBs use permanent magnets in both the rotor and the stator with the same polarity to magnetically support the rotating shaft. Repulsion from the same poles in proximity to one another helps the bearing shaft levitate radially in the magnetic field. Since there is no mechanical contact between the stationary and rotating elements of the bearing, the rotor can rotate about its longitudinal axis without any surface-to-surface friction to slow it down, which is typical in fluid film bearings. Due to no mechanical contact, the vibration does not get transmitted to the non-rotating elements of the machine in low radial stiffness applications.
High speed rotating machines operating in harsh environments require PMBs that are reliable, cost effective and have a long operating life. They do not need a lubricant to operate effectively and can also be used in conjunction with active electromagnetic dampers to limit the unbalance response, stabilize rotordynamic modes and lessen housing vibrations and rotational energy dissipation.