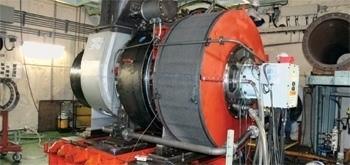
Electrically Assisted Turbocharger for Ships Using Permanent Magnet Motor Technology and a Variable Speed Drive
Mitsubishi Heavy Industries, Ltd. (MHI), the leading marine equipment manufacturer, was looking for an alternative to auxiliary air blowers to reduce power consumption and operating costs by obtaining more energy from less fuel while remaining compliant with international marine rules and regulations. MHI’s turbocharged diesel engines suffered from inherent deficiencies at low engine speeds as there was not enough energy in the exhaust to produce adequate boost for the engine intake air system especially at off-design points.
MHI and Calnetix Technologies developed a unique system called the Electro-Assist Turbocharger (EAT). The EAT incorporates a compact and highly efficient electric motor that assists the driving of the turbocharger. This provides optimization of plant efficiency, especially when a ship is operating under slow steaming. The EAT enables equal or better performance than an auxiliary blower while consuming little power.
The high-speed permanent magnet motor is directly mounted to the turbocharger in an overhung configuration without requiring an additional set of bearings. The motor applies torque to accelerate the turbocharger’s rotor at low engine exhaust flow rates in order to supply sufficient charge air to maximize engine performance. This technology proves even more important as the majority of large marine vessels are now operating in a “slow steaming” part throttle mode to reduce fuel consumption. To date, the majority of marine diesel engines use auxiliary air blowers (AAB) to supply additional air to the engine intake during off design point operation. These AABs are inefficient and not intended nor designed to be used in constant operation. The EAT unit can provide a higher discharge pressure at the same electrical power consumption as an AAB.
The main challenges addressed in the design of the Electro-Assist Turbocharger (EAT) were power optimization, thermal management and control optimization at the system level.
Tests showed that the electric-assist turbocharger reduced fuel oil consumption and a significant amount of black smoke at engine start up. The EAT provided high efficiency and saved approximately 30% electric power consumption compared to the use of existing auxiliary blowers. The efficient design of the EAT improved fuel efficiency, eliminating the need to run an external piece of machinery during operation, thus lowering maintenance costs. Some of the other advantages of the EAT over auxiliary blowers included:
See what Calnetix’s high-speed solutions can do for your business.